For all your autoclaved aerated concrete (AAC) cladding needs, think Dahlsens. Dahlsens can supply a wide range of AAC panels from CSR Hebel, ideal for homeowners looking for excellent thermal insulation and high levels of fire resistance. AAC wall panels are a lightweight and cost effective material for full wrap or feature applications on both internal and external walls. Manage your cash flow by using your convenient 30 day trade account to purchase your light weight Hebel AAC panels.
NEW – Hebel PowerPanel XL now stocked at Dahlsens Pakenham and Laverton for delivery to job sites across Melbourne and Ballarat!
Our supplier
The Hebel brand was born in 1989, created by the leading Australian brand CSR. CSR is widely recognised as a prolific supplier of high quality building materials for residential and commercial construction applications. in 1989, CSR recognised that there was a gap in the Australian market for an alternative material to the standard masonry products available at the time. Committed to providing aerated concrete products for local builders, CSR created the CSR Hebel brand and built Australia’s first AAC manufacturing plant in Somersby, NSW. The production of Hebel AAC blocks and panels commenced at this plant in 1990.
Over the last 30 years, Hebel aerated concrete products have been used in an impressive portfolio of projects Australia wide including:
- The Melburnian apartment complex in Southbank, Melbourne
- The Nishi building in NewActon Precinct, Canberra
- The Southern Sydney Freight Rail Line, Sydney
- One Central Park apartments, Sydney
As Australia’s only manufacturer of aerated concrete products, Hebel is committed to the ongoing innovation of sustainable aerated concrete blocks and panels designed to improve peoples homes and businesses while being kind to the environment.
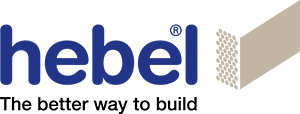
Why choose autoclaved aerated concrete cladding?
High strength performance
Hebel aerated concrete cladding products are reinforced with anti-corrosion steel to provide excellent structural capability and strength. AAC is a high strength product with one-quarter of the density found in regular concrete products.
Excellent thermal performance
Relative to traditional masonry and concrete products, aerated concrete cladding has high thermal insulation properties. As air itself is a poor thermal conductor, the air bubbles present in aerated concrete blocks and panels prevent heat from being easily transferred to the other side. AAC also has naturally airtight characteristics, allowing builders to create airtight building structures which help to prevent heat escaping.
Fast and easy installation
Aerated concrete blocks and panels manufactured by Hebel are lightweight and easy to handle. Installation of Hebel cladding can be performed quickly, allowing you to minimise on site labour costs and delight your clients with rapid construction. Hebel AAC cladding can worked using off the shelf tools for sawing, drilling, machining and nailing.
Sound insulation
AAC blocks and panels have excellent sound insulation properties. They are particularly effective in reducing mid to low frequency sounds thanks to the high surface mass and porous structure of AAC panels.
Ideal fire resistance qualities
AAC blocks and panels are among the highest-rated fire resistant building materials available in Australia. AAC will not explode and is non-combustible. Ideal for buildings in bushfire-prone areas, AAC products typically have high fire ratings and BAL ratings.
Designed for longevity
Like normal concrete, AAC blocks and panels are long lasting and durable. When used in conduction with an appropriate surface coating, aerated concrete cladding is resistant to moisture, rot and termite damage. It is able to withstand the harsh Australian elements better than many other comparable building materials.
Rigorously tested
Hebel are the aerated concrete experts. Their AAC block and panel products have undergone extensive and rigorous quality testing to ensure consistently high quality standards with low associated risks. All Hebel AAC panels are compliant with the Australian Standard for Reinforced Autoclaved Aerated Concrete (AAC), AS 5146.
A sustainable choice
Autoclaved aerated concrete blocks and panels help buildings meet NCC and state specific energy efficiency targets with its airtight and thermal insulation qualities. Using AAC blocks and panels can also help buildings to receive credits under sustainable building certificate programs and schemes such as:
- GreenStar
- LEED (Leadership in Energy and Environmental Design)
- NABERS (National Australian Built Environment Rating System)
Eco-conscious clients will appreciate that autoclaved aerated concrete blocks and panels result in less embodied energy and emissions over time when compared to a normal concrete block or panel.
Non toxic
Hebel autoclaved aerated concrete blocks and panels do not contain any toxic substances and will not harbour or attract vermin.
Versatile applications
Hebel autoclaved aerated concrete blocks and panels have an extensive range of suitable applications. If you enjoy working with a consistent building material across projects, aerated concrete is not limited to cladding. AAC can be used for applications such as:
Residential houses, multi-residential builds and apartments
- External walls
- Zero party walls
- Intertenancy and party walls
- Corridor walls
- Shaft walls
- Services walls
- Floors
- Fences
- High rise facades
- Balcony blades
Civil and utilities
- Fire walls
- Acoustic / Firewalls
- Sound barriers
Commercial and industrial
- External walls
- Internal walls
- Fire tunnels
- Intertenancy walls
- Corridor walls
- Shaft walls
- Services walls
- High rise facades
- Balcony blades
- Floors
Autoclaved aerated concrete cladding available at Dahlsens
Hebel PowerPanel50
Hebel PowerPanel50 is an AAC panel cladding solution reinforced with anti-corrosion coated steel.
Hebel PowerPanel50 features:
- Square edge profile
- Good thermal insulation properties
- Great acoustic performance
- Non-combustible
- Low maintenance
- BAL FZ rated
- Fire rated up to 90 minutes
Available sizes:
- 600 x 2400 x 50mm
- 600 x 2550 x 50mm
- 600 x 2700 x 50mm
- 600 x 2850 x 50mm
- 600 x 3000 x 50mm
Hebel PowerPanel50 can also be made to measure to minimise cutting required on site.
Installation and maintenance:
Hebel PowerPanel50 can be installed quickly and efficiently. One standard Hebel cladding panel is equivalent to 75 traditional bricks, meaning that with Hebel, the external walls of a 150m2 home could conceivably go up in as little as three days.
- Light weight and easy to handle
- Fix to conventional frame walls of timber or steel via metal top hats
- Suitable for internal and external applications
- Termite and rot resistant
- Maintain as recommended by the coating manufacturer
Hebel PowerPanelXL
For an AAC cladding solution with a more substantial structure, think Hebel PowerPanelXL. With the same anti-corrosion coated steel reinforcement as the Hebel PowerPanel50, the Hebel PowerPanelXL is a thicker panel with a width of 75mm instead of 50mm. Clients in bushfire prone zones will enjoy the peace of mind that comes from a higher fire rating and highest BAL rating. Designed for maximum durability, Hebel PowerPanelXL is made to last.
NEW – Hebel PowerPanel XL now stocked at Dahlsens Pakenham and Laverton for delivery to job sites across Melbourne and Ballarat! Download more information here.
Hebel PowerPanel50 also features:
- Square edge profile
- Excellent thermal resistance
- Great acoustic performance
- Non-combustible
- Low maintenance
- BAL FZ rated
- Fire rated up to 90 minutes
Available sizes:
- 600 x 2400 x 75mm
- 600 x 2550 x 75mm
- 600 x 2700 x 75mm
- 600 x 2800 x 75mm
- 600 x 2850 x 75mm
- 600 x 3000 x 75mm
- 600 x 3300 x 75mm
Hebel PowerPanelXL can also be made to measure to minimise cutting required on site.
Installation and maintenance:
Like Hebel PowerPanel50, Hebel PowerPanelXL easy to install and maintain.
- Light weight and easy to handle
- Fix to conventional frame walls of timber or steel via metal top hats
- Suitable for internal and external applications
- Termite and rot resistant
- Maintain as recommended by the coating manufacturer
Autoclaved aerated concrete manufacturing process
AAC is used widely on construction sites all over the world, and the technology to produce commercial quantities of AAC was developed more than 70 years ago in Scandinavia. The raw materials used in AAC production are sand (silica), lime, cement and water.
Mixing
The raw materials are mixed and combined with an expansion agent. Each manufacturer may differ in the expansion agent used, although small amounts of aluminium paste or powder are popular choices. Once mixed, the result is a semi-liquid product called ‘slurry’.
Moulding
Manufactures use moulds to form AAC blocks or panels. If a reinforced panel is being created, the steel mesh reinforcement will be placed into the mould while it is empty. Any anti-corrosion coatings or similar protections are applied to the steel prior to this placement. Once the mould is suitably prepared, the slurry mix is carefully poured into the mould.
Chemical reactions
When the slurry is poured, a series of chemical reactions take place between the raw ingredients. These chemical reactions cause hydrogen to form, which then causes the slurry mix to rise in the mould. When the hydrogen gas dissipates, it leaves behind a large number of tiny, finely dispersed air pockets. These air pockets are the key factor for how AAC is so much lighter than traditional concrete, while remaining strong and retaining excellent thermal insulation properties. This stage is called the ‘pre-curing’ stage.
Cutting
When the slurry has become more solid (but is still soft and malleable), it is removed from the moulds. The resulting product is cut as needed in order to ensure all panels and blocks are the correct size. Any waste created at this stage is recycled.
Curing
Finally, the now consistently sized blocks and panels are baked under high levels of heat and steam pressure. This hardens or ‘cures’ the mix, which is the final step in the AAC manufacturing process.
Sustainable manufacturing at Hebel
The manufacturing process of ACC is eco-friendly when compared to traditional masonry products commonly used in construction projects. All green waste from the pre-autoclaved Hebel products are returned to the green mix for reuse. AAC makes excellent clean fill and road base, so it is able to be easily recycled and repurposed post-autoclaving as well.
Hebel are committed to ongoing sustainability practices and innovation.
The Dahlsens difference
Here at Dahlsens, we’re with you every step of the way. From providing expert advice right through to delivery and installation, your dedicated Dahlsens representative will be your single point of contact.
In addition to our convenient 30 day trade accounts, we offer flexible pick up and delivery options to suit your schedule. You can choose to pick up your aerated concrete building materials at one of our express drive through locations at a time that suits you. Prefer delivery? We can schedule your deliveries to arrive on site according to your project schedule, eliminating extra storage or security costs.
Need some advice?
If you’re new to aerated concrete products or aren’t sure which option is right for your project, we’re here to help. The Dahlsens team of experts can provide professional advice to help you choose the right product for every job. For more detailed advice, simply send us your project plans and we can make recommendations for materials, products and even colours to suit every budget and application.
Warranties
Here at Dahlsens, we know that your time is valuable. We pride ourselves on maintaining excellent relationships with our suppliers and in the unlikely event that you experience a quality issue with any of your Dahlsens supplied AAC products, we put those relationships to work. Simply contact us with a few details about the issue you’re experiencing, and we’ll take care of the rest. Forget spending hours on the phone organising a warranty repair or replacement. With Dahlsens, you can focus on your construction site knowing that we’re negotiating a winning solution with the supplier on your behalf.
Aerated concrete cladding FAQs
Reinforced AAC Standards (AS 5146:2015 Parts 1-3)
In 2015 Standards Australia approved and published a set of standards for reinforced AAC, known as AS 5146:2015 (Parts 1-3). These standards help guide the use of reinforced AAC in designs and construction within Australia.
AS 5146 (Parts1-3) were referenced in the Building Code of Australia in May 2016, making Reinforced AAC a ‘deemed to satisfy’ (DTS) building material. This means that if builders and installers construct a building using the details provided in AS 5146, (Part 3), it should make for easier certification of the building by the relevant building certification authority. All Hebel products and systems are compliant with AS 5146 (Parts 1-3).
What is AAC?
Autoclaved Aerated Concrete (AAC) is a versatile, strong lightweight building product.
Can aerated concrete cladding help reduce energy costs?
Yes, aerated concrete cladding provides excellent thermal insulation, which helps regulate indoor temperatures. This can reduce heating and cooling costs, making it an energy-efficient choice.
How is aerated concrete cladding installed?
Aerated concrete cladding is usually installed as prefabricated panels attached to the building’s exterior. These panels are secured with specialised fixings, and a finish such as render, paint, or other coatings can be applied to achieve the desired appearance.
Is aerated concrete cladding resistant to moisture?
Aerated concrete has some moisture resistance, but it is porous and should be properly sealed or finished to prevent water absorption. Applying a protective coating, such as paint or render, helps increase moisture resistance.